Everything Is a Materials Problem

Our group studies the interplay between mechanics and architecture at the nanoscale to create new classes of nanoarchitected materials with unprecedented mechanical properties. Our goal is to utilize the exceptional behaviors of nanomaterials — like ultrahigh strength and toughness, radiation damage tolerance, and enhanced ductility — using a range of micro- and nanoscale fabrication and testing methods. We have shown that nanoarchitected materials can attain remarkable properties. Examples include ceramics that are able to bounce back after compression to over 50% strain and fractal-like architectures that can localize failure to tune the mechanical response.
Our work is often bioinspired in nature, as the techniques we use can approach and replicate the length scale and complexity of natural materials. We are currently interested in the general areas of materials for extreme environments (irradiation, high temperature, ballistic impact, etc), multifunctional materials with combined mechanical, electrical and thermal performance, and biocompatible materials for operation in medical devices.
We use two approaches in conducting our research:
Materials from the bottom up
We use a suite of advanced 3D micro- and nanofabrication techniques to create new materials with features that are controllable on ~10nm length scales. We apply these nano-“building blocks” to make architectures starting at fundamental material length scales and investigate how this can bring about novel behaviors at micro-, meso- and bulk scales. Our research utilizes the Washington Nanofabrication Facility (WNF) and Molecular Analysis Facility (MAF) at UW along with a set of custom-built equipment. This topic encompasses work on nanolattices, tough nanoarchitectures and metamaterials.
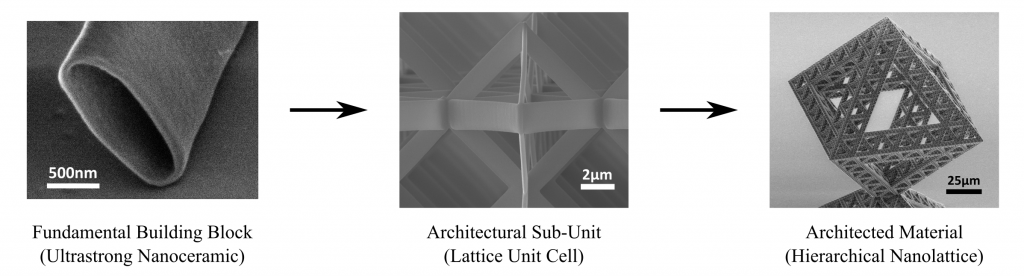
Materials from the top down
The properties of natural and engineering materials are governed by a complex interaction of materials and architecture starting at the nanoscale and moving up. Unraveling the nature of these multi-scale interactions is a fundamental problem in material science. Our work studies the mechanics of materials starting from their nanoscale constituents and investigates how their structure (or architecture) at nano-, micro- and meso-scales affects their large-scale properties. This topic encompasses work on carbon fiber composites, biomaterials and artificial tissues.
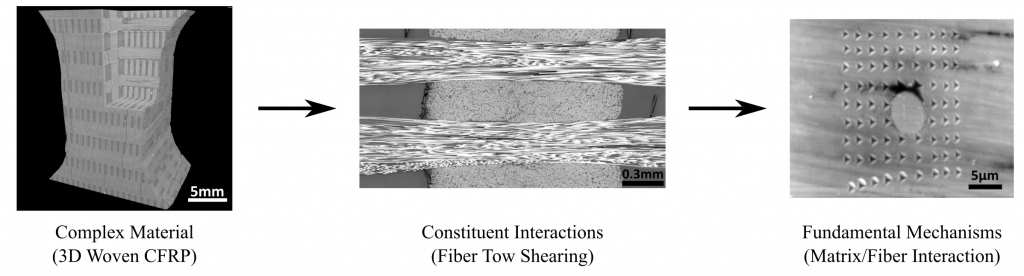
Past Projects
For past projects click here.
Current Projects
Nanofoams
Team Members: Santhosh Sridhar, Kush Dwivedi, Keith Neale, Nathan DeRuyter, Luke Haunreiter, Shaunak Deshpande
Past Members: Zainab Patel, Madeline Waite, Chester Wong, Kellan Yoshikawa, Ryleigh Weston, Basam Khan
Funding Agency: NSF Award #2032539
Primary Goal: To understand why nanofoams are tougher than microfoams. We use experiments at the macro- and microscale paired with numerical modeling to understand the physics of why nanofoams are more resistant to cracking.
Broader Impacts: Lighter, tougher plastics means less plastic waste. Understanding why they are tough means we can apply that learning to other materials (like biodegradable polymers). There are many technological applications of these materials from medical meshes to filters to coffee cups.
Sub-projects:
ISoFoAM
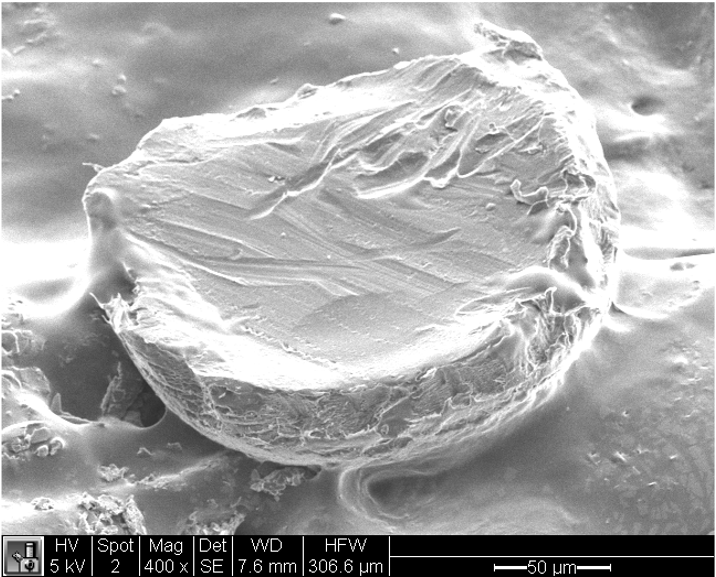
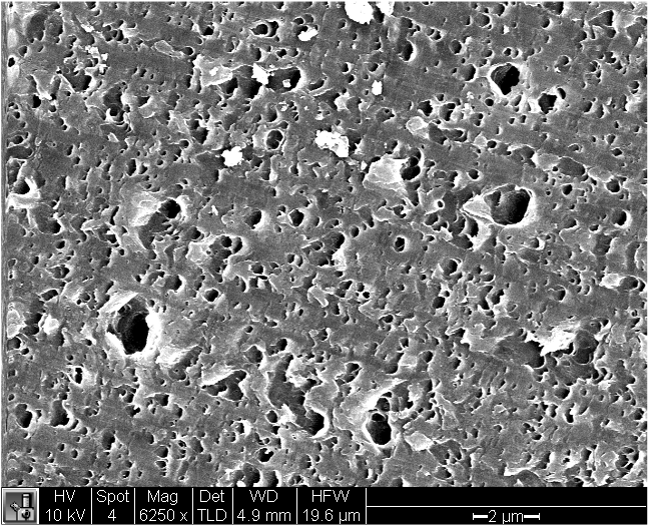
Nanoscale Tensegrity-Based Metamaterials
Team Members: Amitha Rani, Alex Cong
Past Members: Caelan Wisont, Robert Verdoes, Zainab Patel, Matt Leahy, Reese Taylor, Paul Fallon
Primary Goal: Create prestressed tensegrity architectures at the nanoscale. This method would allow for the creation of controllable stress networks within parts.
Broader Impacts: Prestress can be used to control mechanical properties (stiffness of tensegrities) and mechanical resilience (high strength tempered glass or gorilla glass). We are developing a method that can be broadly applied to new materials systems that display size-affected shrinkage.
Sub-projects:
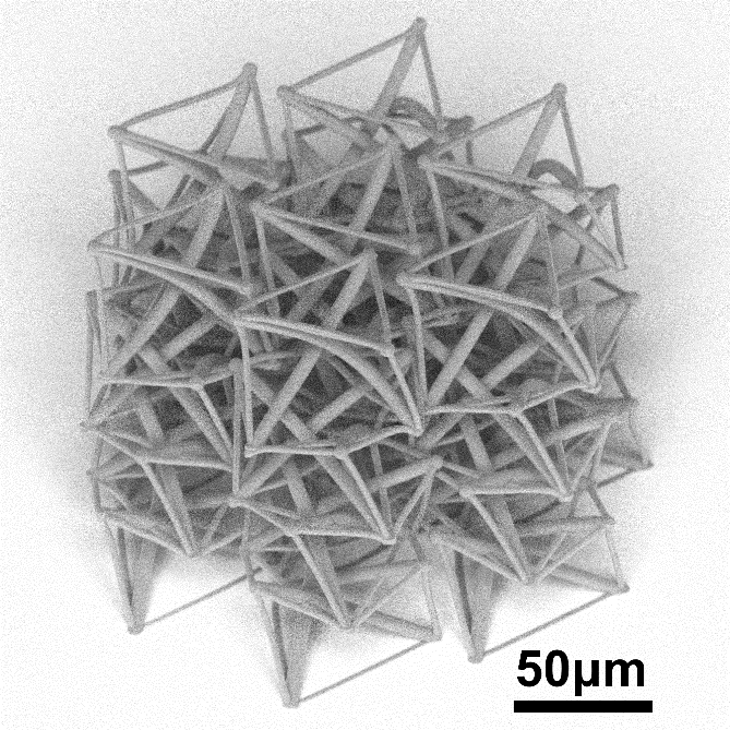
Nanotough Mechanisms in Bioinspired Nanoarchitected Materials
Team Members: Abdulaziz Alrashed, Kush Dwivedi, Basam Khan, Michael Richeson, Andrew Gladnick
Past Members: Zainab Patel, Kevin Nakahara, Ganesh Swaminathan
Collaboration Partners: Brad Boyce, Ben White, Bryan Kern
Funding Agency: Sandia CINT User Facility Grant
Published Works: Toughness Amplification via Controlled Nanostructure in Lightweight Nano-Bouligand Materials
Primary Goal: Uncover the relationship between toughness and nanostructure. Develop nanoarchitectures that use nanomaterials with size-enhanced properties to improve their toughness.
Broader Impacts: This work creates fundamental knowledge into how materials break starting at the nanoscale. It helps us to understand everything from tough engineered materials to natural nanostructured materials.
Sub-projects:
Nano-scale Fracture Toughness of Interpenetrating Lattices (IPL)
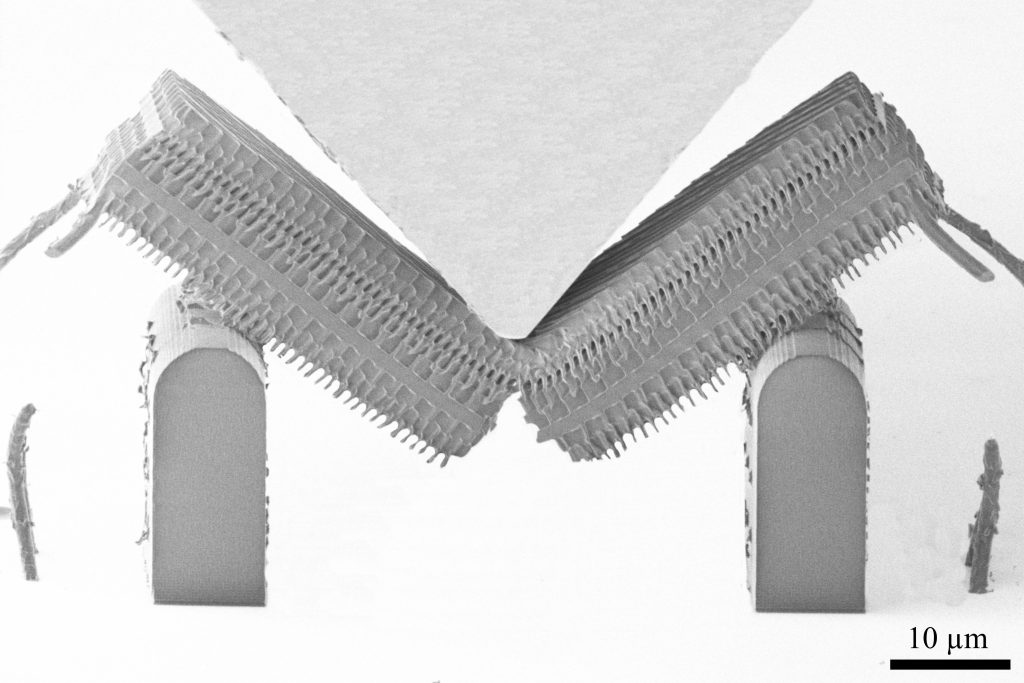
Nanoarchitected Metamaterials with Engineered Recovery
Team Members: Andrea Exil, Amitha Rani, Carter Eldridge
Past Members: Camila Kang, Hallie Wall
Primary Goals: Use origami at the nanoscale to create flexible nanostructured materials. Understand emergent bistability in origami without a soft hinge.
Broader Impacts: Origami provides a framework for flexible and deployable structures. By utilizing principles of origami at the nanoscale, we can create resilient and flexible nanostructures for “smart” materials that can change shape and store mechanical memory.
Sub-projects:
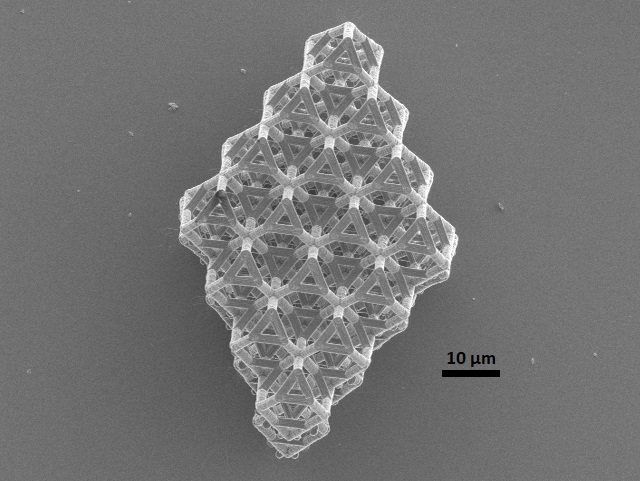
Nano-origami Shape Memory Hydrogels
Team Members: Amitha Mulastham
Primary Goals: Design and fabricate unique metamaterials with architectures based on the waterbomb origami structure. Hydrogels exhibiting shape memory through reversible cross-links that are sensitive to stimuli and switch between two stable configurations upon the application or release of a compressive force.
Broader Impacts: Successful replication of this behavior would enable us to use this technology in stimuli-triggered actuation, drug delivery, and production of membranes with variable permeability.