Constrained Foaming
Microcellular technology has evolved around thin-walled applications.  Can the microcellular process be scaled up to make thick parts for load-bearing applications?  In an effort aimed at producing lightweight and energy efficient panels for housing construction, our laboratory has produced 10 mm thick ABS sheets with 50% or higher reduction in density in a constrained- foaming process illustrated in Fig. 1.  The key difference from the batch process is that the foaming is done inside a heated press in order to keep the foamed specimen flat.  Fig. 2 shows a schematic of the gradient microstructure across the panel thickness.  The foaming step can be carried out in matched heated mould to attain a contoured shape.  A key focus of the current research is to reduce the saturation time for thick sheets to make the process more cost-effective.
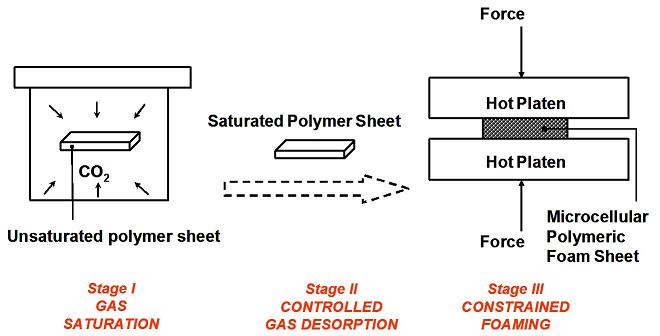
Figure #1: Constrained Foaming Process
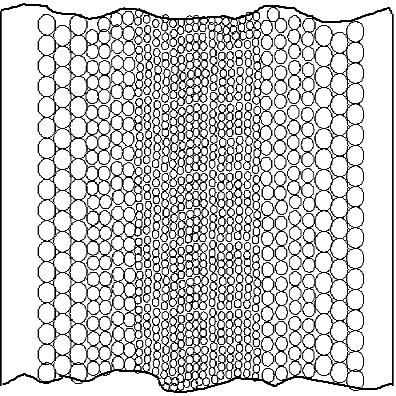
Figure #2: Schematic of the gradient microstructure of a microcellular panel.